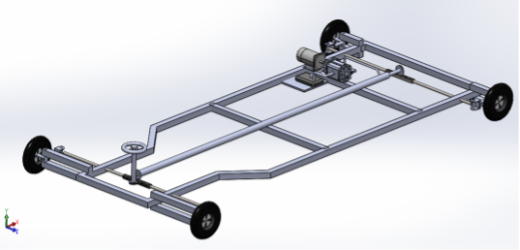
Rear Wheel Steering
Design of Rear-wheel steering system
The rear wheel steering model which is done using SOLIDWORKS s. The specifications of Maruti Suzuki Alto K10 is considered for designing purposes which are listed below,
Top speed: 145 kmph
Wheelbase: 2360 mm
Wheel Size / Wheel Diameter: 13 inch
Front Trackwidth: 1295 mm
Rear Trackwidth: 1290 mm
Turning Radius: 4.6 m
Gross Weight: 1210 kg
This model is based on Rack and Pinion mechanism for actuation. It consists of four wheels whose wheel diameter is 13 inch, connected to the vehicle chassis using control arms. The wheels are connected to the rack by a connecting arm. A shaft consisting of pinion on both the ends is attached between the two racks. There are two steering rack present - one for the front wheels and other for the rear wheels. The front rack is designed in such a way that gear teeth is provided on two sides - one on the top surface for meshing with the pinion of the shaft and other on the front surface for meshing with the pinion of the steering column. The rear rack has gear teeth only on its top surface so that the pinion on the other side of the shaft is meshed. A steering column along with a pinion at its one end is meshed with the front surface of the front rack and the other end in connected with a steering wheel. So that when steered, the rotational motion of the steering wheel is converted into linear motion in the front rack, thus making the front wheels to be steered. Since a shaft with the help of pinion on both sides is connected between the two racks, when the front rack is moved, the rear rack will also move. Thus making the rear wheels to be steered in the opposite direction. For example, when the front wheel is steered towards left, the rear wheel is turned towards right and vice-versa.
The basic working of the solenoid actuated 3/2 spool valve is, the oil supply from the pump is connected to the inlet port shown in fig.2. The outlet port is connected to the shaft vent. The exhaust port is connected to the oil reservoir so that the same oil is used again. Initially the inlet port is closed, when the spool is actuated, the inlet port opens and the oil flows through the outlet port into the shaft vent while the exhaust port is closed by the spool. This is called the working position. Now when the solenoid is de-energized, the spool returns to its rest position and the inlet port is closed so that the exhaust port is opened and the oil from the shaft returns back to the reservoir. This is called the normal position.
Project Numbers
1
Mentors
2
Members